Anisoprint Composer: 3D-печать композитами высокой прочности
Здравствуйте! Сегодня вы узнаете о преимуществах и тонкостях работы с композитными материалами, в том числе и в 3D-печати.
Почему обычные угленаполненные пластики не задают печатаемому изделию свойства карбона? Как должны располагаться волокна в материале для наибольшей прочности принта? В чем новизна подхода “Анизопринта” к печати композитами и почему на него стоит обратить внимание?
Представленный материал — лекция Фёдора Антонова, генерального директора компании “Анизопринт”, с которой он выступил на Top 3D Expo.
Видео
Выступление
О чем речь
Здравствуйте! Меня зовут Федор, я очень люблю говорить о композитах и расскажу о том, для чего используются композиты, в чем их преимущество; и немножко расскажу причем здесь 3D-печать и как это можно вместе комбинировать.
3D-печать, как все знают, относится к аддитивным технологиями. Технологии изготовления композитов, появившиеся задолго до 3D-печати, с самого начала были также аддитивными. Таких технологий много. Но то, что делаем мы сейчас, в новинку и для производства композитов, и для 3D-печати, то есть — для аддитивной области вообще.
Сравнение с металлами
Я начну как раз с небольшого рассказа про композиты, в частности — про углепластик, в просторечии карбон, который еще называют королем композитов. В чем его преимущества по сравнению с металлами. Для примера можно взять какой-нибудь авиационный алюминиевый сплав и посмотреть на его характеристики.
У него есть плотность, нас также будет интересовать, например, временное сопротивление или прочность.
Есть однонаправленный углепластик, который почти в два раза легче и в пять раз прочнее, чем алюминий. Таким образом получается, что удельная прочность однонаправленного углепластика, по сравнению с алюминием, в 10 раз выше.
Если мы будем сравнивать с какой-нибудь сталью, даже самой крутой, то разница будет еще больше — потому что сталь очень тяжелая. Поэтому все в свое время влюбились в углепластик и стали делать из него высоконагруженные ответственные конструкции — в начале в ракетах, потом в самолетах, сейчас в машинах и уже в ряде потребительских товаров используется этот уникальный материал.
Особенности
Углепластик — это композит, одной из основных особенностей которого является то, что все вот эти уникальные свойства, вся прочность у него вдоль направления армирования, вдоль волокон. В поперечных направлениях свойства на два порядка ниже.
Как инженеры карбон “исправляли”
Почему-то люди решили, что векторность углепластика является большим недостатком, стали думать как от этого избавиться. Слои однонаправленного углепластика стали укладывать друг на друга под разными углами, чтобы получить так называемый квази-изотропный ламинат, который инженеры, работающие в этой области, любят называть “черным алюминием”.
Как мы видим из названия, по свойствам он как листовой алюминий, используется примерно в таких же конструкциях: фюзеляж самолета, крыло, корпус ракеты. После того, как свойства углепластика “размазали” в разные стороны, его прочность стала примерно в 10 раз меньше. То есть — приблизилась к обычному алюминию.
И сразу мы потеряли все замечательные преимущества, которые имели у однонаправленного углепластика, но при этом получили массу проблем связанных с технологией, с ударной прочностью, особенностями разрушения, с соединениями таких узлов между собой. Там целый спектр сложных проблем. Поэтому в последнем поколении гражданских самолетов было от 50 до 60 процентов композитов, а в следующем поколении, как говорят эксперты в индустрии, их будет как минимум в два раза меньше. Потому и программа “Dreamliner” абсолютно провальная получилась у Боинга. Все те надежды, которые в авиации возлагали на композиты, не оправдались именно из-за попыток сделать углепластик “всенаправленным”.
Другой подход
А есть и другой подход. Он отличается от “черного алюминия”. Из композитов очень эффективно делать так называемые сетчатые конструкции, такие как “Шуховская башня”. Вот здесь, наверху, изображен адаптер полезной нагрузки ракеты-носителя “Протон-М”, который сделан из углепластика, но не из “черного алюминия”, а в виде сетчатой конструкцию с ребрами определенного направления и определенной плотности. Деталь весит около 50 килограмм и выдерживает нагрузку 200 тонн. Аналогичная деталь, под те же самые нужды, сделанная из сэндвича углепластика, весит на 30 процентов больше и выдерживает меньшую нагрузку. С алюминиевыми все еще хуже.
В такой конструкции композит работает только вдоль волокон. У него нет возможности работать поперек, поэтому все его анизотропные свойства используются так как надо.
Fiber steering
Есть еще одно интересное направление, помимо сетчатых конструкций, называется “Fiber steering”. Это когда мы волокна укладываем не под фиксированными углами прямолинейно, а по криволинейным траекториям, таким образом, чтобы направления волокон в каждой точке соответствовали направлениям векторов главных напряжений в детали.
Это панель фюзеляжа самолета с досмотровым отверстием. Она была изготовлена методом автоматизированной выкладки. Сейчас это некоторые тоже называют 3D-печатью, хотя этой технологии несколько десятков лет и она давно и активно используется для изготовления деталей из композитов. Вот по таким криволинейным траекториям.
Были проведены сравнительные испытания таких деталей и “черного алюминия”. Вот эта панель, файбер-стиринговая, при том же весе и характере нагрузок, выдерживает на 30 процентов большую нагрузку на сжатие. При этом видно, что совершенно другой характер разрушения. Такая панель работает гораздо более эффективно.
Задачи
Одна из наших основных идей заключалась в том, чтобы дать возможность инженерам-конструкторам изготавливать, производить и проектировать действительно эффективные конструкции из композитов. Уходить от “черного алюминия” и делать так, чтобы анизотропия материала из недостатка, как многие считали, стала главным преимуществом этого материала. То есть, мы говорим что изотопный материал это хорошо, потому что зная. как работает деталь, зная условия нагружения, расчетные случаи, зная внутренние усилия и напряжение мы можем в каждой точке фокусировать свойства материала, именно в том направлении, в котором это нужно. Таким образом, у нас получается целое дополнительное пространство для оптимизации. Мы можем оптимизировать не только форму деталей, но и их внутреннюю структуру.
Почему 3D-печать
К сожалению, традиционные автоматизированные технологии изготовления деталей из композитов не позволяют вот так, произвольно в каждой точке, укладывать волокна. Когда мы только начинали заниматься этой темой, которая выросла в тот продукт, который мы сегодня, в том числе, представляем на этой выставке, она выросла из той идеи, что мы хотим делать композиты, в которых можно произвольно управлять направлением анизотропии и степенью анизотропии в каждой точке материала. Старые технологии этого делать не позволяли. Тогда мы решили посмотреть — что же может нас приблизить к этой цели. И здесь весьма кстати оказались технологии 3D-печати.
Композит, да не тот
Что вообще в мире 3D-печати делается с композитами. Самое простое, с чем все знакомы: когда мы говорим, что мы печатаем углепластиком, все говорят, что все печатают углепластиком. Нет, все не печатают вот таким углепластиком. Обычно это пластик наполненный рубленными волокнами, по сути — обычный пластик с наполнителем, изотропный материал, в котором мы никаким направлением этих волокон не управляем.
Это, конечно, тоже интересная вещь, но никаких свойств, даже близко приближающихся к свойствам настоящих композитов, здесь нет. Материал получается чуть более, ну — в два-три раза, более жестким, чем обычный пластик. Иногда он может быть чуть прочнее. Он гораздо лучше себя ведет при усадке. Вот эти технологии, например, успешно используются для печати крупногабаритных деталей — там по несколько метров. Но ничего нового, именно с точки зрения проектирования и с точки зрения технологии в целом, этот подход не дает. Это обычный FDM, или, как в этом случае, SLS, когда мы в полиамидный порошок добавляем мелко рубленное волокно.
Если говорить о свойствах, да — у OXFAB, это SLS-машина для печати композитов, заявленная в плоскости прочность принтов 110 мегапаскалей, а у обычного полиамида, не наполненного, где то 40-50. Да, это лучше, чем обычный пластик, но не на порядок.
Кроме рубленых волокон, есть интересный вариант с волокнами длинными, например — технологии ламинирования. Я знаю штуки три или четыре, наверное, но тут я скажу об одной. Я не знаю, честно говоря, какова судьба этого проекта. Пару лет назад EnvisionTEC его в качестве прототипа показывал на FormNext по-моему. Это не совсем аддитивная технология.
Берутся листы заранее пропитанной термопластом углеродной ткани, так называемые “препреги”. В одной зоне этот лист раскраивается по контуру слоя, возможно ультразвуком, в другой зоне потом он прикатывается, ламинируется, таким образом формируется слой. Вот это — чистой воды “черный алюминий”, только изготовленный на специальной машине. То есть, это такой квази-изотропный материал, в котором есть все недостатки “черного алюминия”, такие как разрыв волокон и, как следствие, концентрация напряжений, и краевые эффекты, которые приводят к тому, что очень слабыми местами становятся отверстия и места соединений.
Следующий шаг, чуть ближе к тому, что мы начали делать — это такая экструзия термопласта с непрерывным волокном. По сути — это FDM технология, только в процессе печати в сопло непрерывно добавляется армирующее волокно. Довольно много научных групп во всем мире подобными вещами занимаются.
Здесь проблема в том, что конструкционные волокна не являются мононитью, они состоят из сотен или тысяч микронных нитей, и если мы просто добавляем вот это вот волокно в расплав вязкого пластика, он не попадает внутрь, не пропитывает волокно и композит не формируется. Внутри получается одна большая пора. Не получается композит, потому что в композиции должно быть армирующее волокно и связующее вещество, которое соединяет все компоненты между собой, заставляя их работать вместе. В этом случае этого не происходит. Поэтому, хоть прочность на растяжение может быть достаточно большой, на сжатие никаких особых характеристик в таких материалах нет. Если смотреть на микроскопию, внутри очень много пор между волокнами.
Второй подход, чуть более удачный, я его называю “выкладка препрега” — это когда мы берём то же самое волокно, например углеродное или стеклянное, и заранее, на специальной установке, пропитываем его вязким пластиком под большим давлением, либо вымачиваем в растворе и потом выпариваем, и протягиваем через фильеру.
То есть, мы пытаемся заранее, на специальной машине, поместить этот вязкий пластик внутрь волокна. На выходе получаем пропитанную нить, которая традиционно в композитной отрасли называется “препрегами”. То есть — полуфабрикат для изготовления композита. И дальше мы этот “препрег” через сопло разогреваем и экструзией или выкладкой формируем деталь.
Самый известный, наверное, в мире 3D-печати пример, когда люди печатают непрерывным волокном — это американская компания Markforged. Они уже довольно давно вот эти свои системы продают. Это тоже выкладка препрега. У них тоже присутствует заранее пропитанное нейлоном углеродное волокно и сопло, в котором оно разогревается и которым выкладывается. И есть еще дополнительно пластиковое сопло, для печати просто пластиком. У принтов Markforged достаточно хорошие характеристики. Прочность уже свыше 700 мегапаскалей. Есть выбор типов армирующих волокон. Но, как мы видим по количеству пор, и есть масса статей, где исследуется микроструктура этих материалов, количество пор очень большое. То ли из-за того, что пропитка плохая, то ли из-за того, что это нейлон и он набирает воду и при печати вскипает.
Технология Анизопринта
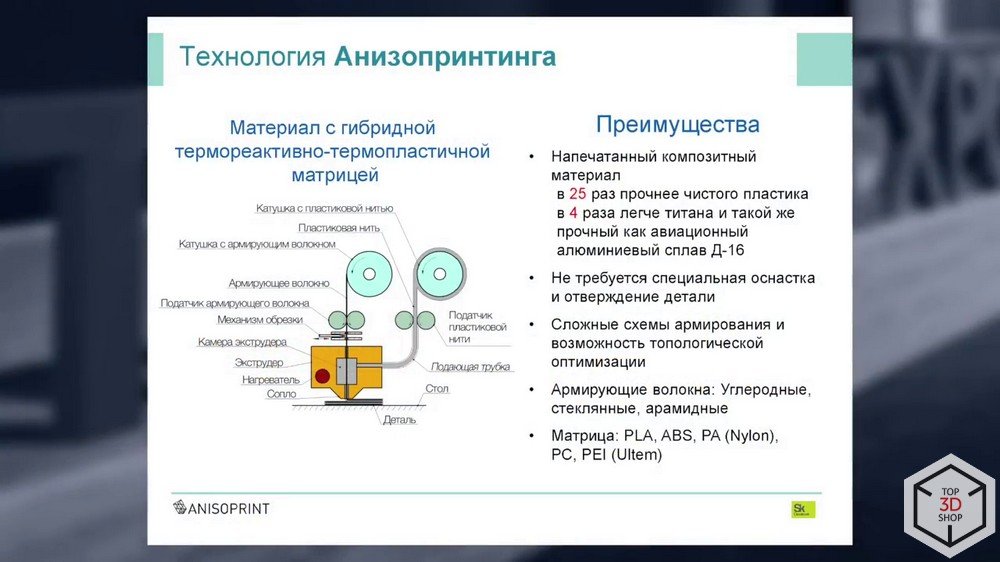
Мы заранее пропитываем волокно, но не термопластом, а реактопластом, что позволяет обеспечивать более качественную, более дешевую, более надежную пропитку этого волокна. И такой процесс мы уже называем коэкструзией. Так как такое волокно уже расплавить нельзя, в процессе печати мы к нему добавляем отдельно пластик. И на выходе получается двухматричный композит, в котором внутри волокна у нас есть не расплавляемый реактопласт, который обеспечивает пропитку волокна, а между волокнами у нас есть термопласт, который их между собой связывает.
В нашем случае этот пластик может быть любым. Если вам нужен негорючий пластик, или цветной, или пластик со стойкостью к определенным химическим или температурным воздействиям или окружающей среде — вы можете выбрать тот пластик, который вам подходит. Потому что все основные поверхностные свойства материала определяются именно связующим — матрицей. И мы можем, за счет того, что у нас раздельно подается волокно и пластик, в каждой точке локально менять объемную долю волокна и пластика. Мы можем подавать меньше пластика — тогда у нас увеличивается объемная доля волокна, можем подавать больше пластика — тогда она уменьшается. Таким образом мы можем управлять степенью анизотропии и, что более важно, печатать сетчатые конструкции с пересечениями волокон внутри одного слоя. То есть, мы можем укладывать армирующие волокна друг на друга, под любыми нужными нам углами, в пределах каждого слоя индивидуально. При этом у нас не растет толщина слоя в месте пересечения, у нас изменяется только объемная доля волокон в этом самом месте.
Тут очень много плюсов. Такой рекламный самоуверенный слайд. В 20 раз прочнее пластика, в два раза прочнее алюминия, сильно дешевле печати металлом. Всё, что я говорил про оптимизацию, автоматизацию, чистоту — все это для этой технологии тоже свойственно, впрочем, как и для некоторых технологий конкурентов.
Еще один рекламный слайд, который я уже давно показываю на всех конференциях. Если мы берем по оси абсцисс стоимость оборудования, по логарифмической шкале, а по оси ординат удельную прочность материала, то есть прочность отнесенную к удельному весу — то все металлы печатаемые по технологии SLM у нас оказываются внизу графика, а самым лучшим из них оказывается титан.
Оборудование и ПО
Anisoprint Composer
- Размеры, мм: 600х400х375;
- Вес, кг: 25;
- Программное обеспечение: Anisoprint Aura (FFF+CFC), Cura, Slic3r (только FFF);
- Материал: PETG;Carbon Fiber;PLA;ABS;Нейлон;ПК и т.д.;
- Подогреваемая платформа: стекло с подогревом;
- Рабочая камера: 279х210х147 мм;
- Температура печатного стола: 20-120 °C;
- Температура экструдера: 250 ˚C;
- Технология печати: FDM; CFC;
- Толщина слоя: от 60 мкм;
- Диаметр нити: 1,75;
- Интерфейсы: SD, USB;
- Количество печатающих головок: 1;
У нас это все запатентовано, естественно, вся эта технология.
Anisoprint Aura
Для этих принтеров мы создали собственное специализированное программное обеспечение, которое называется “Анизопринт Аура” — это слайсер, вы можете управлять армированием, задавать пластиковый периметр и пластиковое заполнение, композитные периметры, композитное заполнение, поддержки, в общем — весь функционал обычного слайсера, плюс функционал для работы с армирующим волокном.
Здесь закрытый корпус, подогреваемый стол, рама выполнена из фрезерованных алюминиевых плит с рельсовыми направляющими по оси z. Схема CoreXY.
Прототипы и планы
Anisoprint ProM
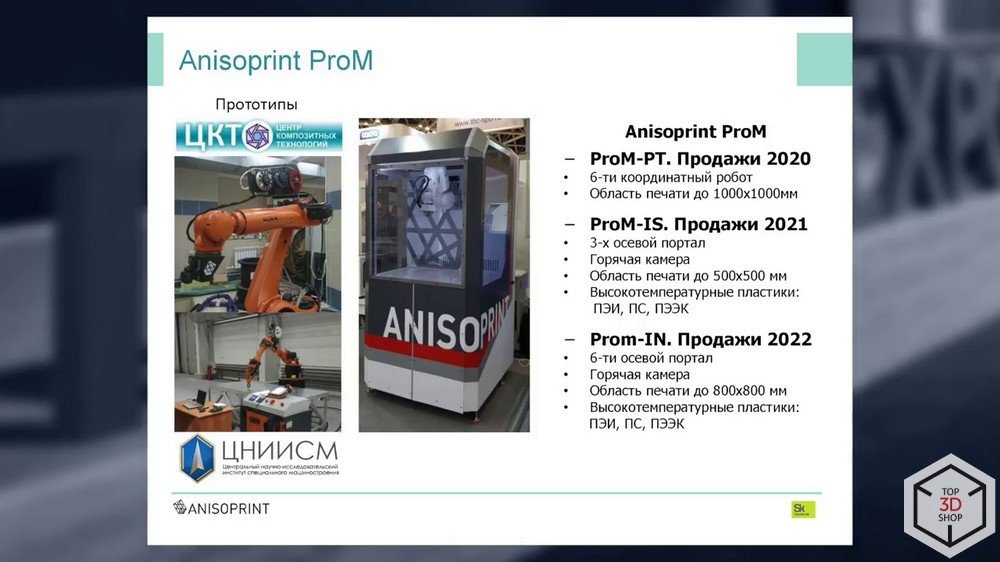
Наша основная цель — это промышленное оборудование для 3D-печати композитов. У нас уже есть некоторое количество прототипов, которые стоят у наших партнеров. Партнеры успешно работают на этих прототипах. Мы уже показывали на выставке металлообработки прототип нашего первого промышленного принтера Anisoprint ProM-PT, который мы еще раз покажем уже в рабочем состоянии, на FormNext, а продажи планируем со второй половины 2020 года. Отличие в том, что в нем шестикоординатный промышленный манипулятор вместо портальной схемы, что позволяет класть волокна не только в плоскости, но и под любыми углами.
То есть, на обычной плоской схеме я могу печатать вот такие детали, где у меня армирование внутри плоскости. Как только мне нужно из плоскости выйти и, допустим, армировать в другую сторону, то тут мне нужно уже иметь дополнительные степени свободы, для чего эта шестикоординатная машина нами и разрабатывается. Помимо того, что здесь промышленный робот, там еще вся промышленная электроника — никаких шаговиков, сервоприводы, контроллер BOSCH, который интегрирован в контроллер робота. Всё это обеспечивает надежность, повторяемость, резервируемость, отвечает промышленным требованиям.
Следующий наш запланированный промышленный продукт — трехкоординатный принтер для печати высокотемпературными пластиками, такими как PEEK и PSU.
Ну и самый топ — это аддитивная машина для изготовления высокотемпературных деталей в шести координатах, но это наша самая долгосрочная цель. Эта технология предназначена для изготовления деталей сложной формы из композитов оптимизированных под под заданную нагрузку и под заданные условия работы.
О конкурентах
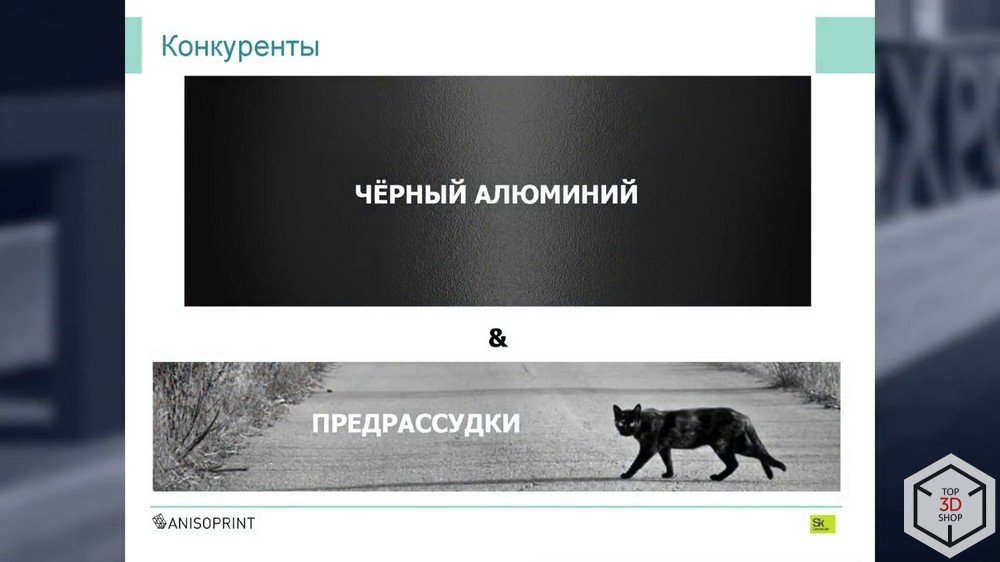
В принципе, такого типа детали из композитов сейчас никакими способами не изготавливаются. То есть, если хотите изготовить такую деталь из композита, наш способ единственный существующий. Остальные технологии изготовления изделий из композитов предназначены в основном для крупногабаритных листовых деталей или профилей, балок, а здесь можно изготавливать детали сложной формы. Но нам также хочется сражаться с металлами, отвоевывать у них долю рынка. Такого типа детали, как кронштейны, элементы соединений, корпуса — все нагруженные детали сложной формы изготавливаются методом фрезерования либо литья. Их мы можем облегчить в разы.
Ну и, раз уж я эту деталь в руках держу — это элемент ножки авиационного кресла, исходная алюминиевая деталь весит 1 килограмм и рассчитана на нагрузку в полторы тонны. Вот это вот — оптимизированная композитная деталь изготовленная нами, спроектированная под те же нагрузки. Она весит 275 грамм — почти в четыре раза легче. И по себестоимости эта деталь будет также дешевле, чем фрезерованная алюминиевая, изготовленная на многокоординатном фрезерном станке.
Еще одно сравнение иллюстрирующее разницу. Она в том, что мы можем обеспечивать надежную пропитку и отсутствие пор в материале, что очень важно для сертификации, для ответственных деталей, для ответственных конструкций. Мы эту технологию называем “анизопринтинг” — это не просто 3D-печать, это разные вещи.
Это довольно важный момент: есть такое очень модное направление в проектировании машиностроительных изделий — называется топологическая оптимизация. Я не буду вдаваться в подробности. В большинстве случаев детали, которые получаются в результате вот этого генеративного дизайна, имеют вид сетчатых конструкций. Естественно, у нас не возникает вопросов, в каком направлении в ребре нужно укладывать волокна. Ребро — это одномерная структура, которая работает либо на растяжение, либо на сжатие, либо на изгиб. Оно не будет работать на поперечный отрыв, потому что это измерение очень мало. Оно не будет работать на межслоевой сдвиг, только при изгибе. Таким образом, свойства в поперечном направлении в ребре, свойства материала поперек ребра, они получаются избыточными. То есть, не имеет смысла эти ребра делать из изотропного материала, потому что поперечные свойства материала там не нужны. Они не нужны такими же, какими они нужны вдоль ребра. Поэтому здесь нужно использовать изотропные материалы. Это самый лучший пример доказывающий преимущества анизотропных материалов перед изотропными.
Примеры и мечты
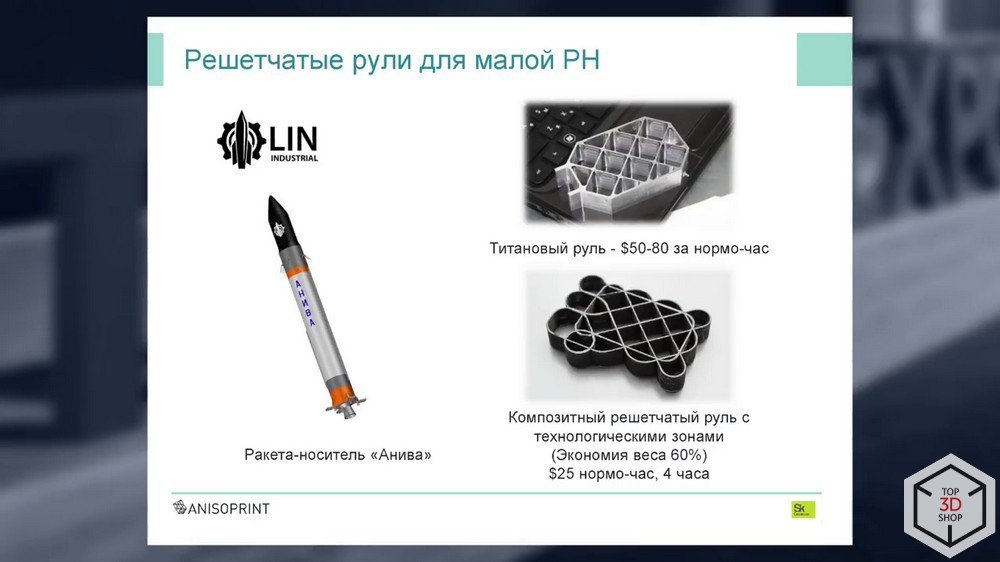
Несколько примеров того, что мы делали, и пару слов про еще более далекое будущее, как мы его видим.
Вот этот самолетик в углу, это концепт Airbus — называется Airbus 2050, здесь художник или дизайнер, наверняка — не инженер, изобразил у самолета сетчатый фюзеляж. Я не знаю, что он вкладывал в эту картинку, но именно такого типа изделия мы хотим научиться делать в будущем. Здесь есть ребра — оптимально использовать композиты. Такая конструкция будет работать наиболее эффективно. Кроме того, что это армирование по произвольным траекториям управления анизотропией, в процессе производства такого вида деталей можно добавлять различные функциональные волокна, функциональные элементы, вставки, электронику. Можно делать адаптивные материалы, добавлять всякие залечивающие агенты. Как-то вот так, на наш взгляд, должно выглядеть будущее производства в долгосрочной перспективе. И, конечно, основным материалом должны быть композиты.
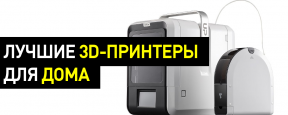
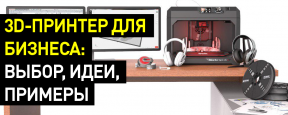
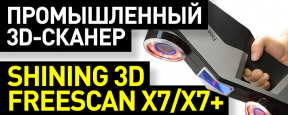
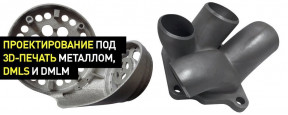
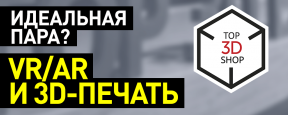
Оставить комментарий